Esco Faced a Number of Challenges to Customize the Rapid Vial Tray Decontamination Chamber (BioPass™)
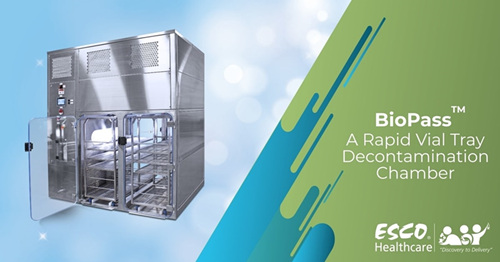
The Project
Esco was recently commissioned to customise a
BioPass™ unit for a large-scale vaccine manufacturer. The project faced a number of challenges.
The main technical challenge for this project is to produce a larger system than previously manufactured, and to design this in a way that will allow disassembly, so it can be installed within a narrow route and space.
Efficient and lean manufacturing practices are of great importance to the client.
The larger unit is integrated with a decontamination system that eliminates further delay for later stage processes.
The final product is a 2.0 m x 1.5 m x 2.0 m (W X D X H) main processing chamber that can accommodate two trolleys heavily loaded with over-bagged vial tubs during each decontamination cycle.
Although the main chamber was required to be larger, restrictions were made on the overall available space on the client’s facility. The addition of features whilst restricting the space for the unit mechanics required extensive design work.
Benefits of the Esco BioVap™ H2O2 Bio-decontamination System
In contrast to the widely-used vaporized hydrogen peroxide, Esco BioVap™ system utilizes an atomised mist of H2O2.
The droplets dispersed themselves evenly across all surfaces within the chamber. The sterilisation process begins once the agent comes in contact with the surface.
Beyond its 6 log reduction in contaminants, this unique process is also unaffected by temperature or relative humidity.
This means that it is not necessary to pre-condition the chamber prior to gassing. With the Esco BioVap™, process efficiency is increased.
The system is linked with active visual indicators for clear display of the unit’s operating mode. There is a white light for normal operation, a steady red light during the gassing process, and a flashing red light to indicate that an alarm has been triggered.
Consequences of Enlarging the Process Chamber
The first challenge Esco needed to address was the ability of the H2O2 to reach all areas, given the increased volume and heavily loaded carts. This was remedied with the inclusion of an additional nozzle to simultaneously vapourise each chamber’s side. Settings were also optimized to produce a finer mist size to increase distribution whilst avoiding any droplet build- up.
The rest of the decontamination system had enough capacity to supply the hydrogen peroxide through dual nozzles without needing to add an additional H2O2system.
Furthermore, the client wanted to use the additional chamber space to process more product with each decontamination cycle. As a consequence, the way in which product was loaded into the machine, became a great concern. As the trolleys are relatively large and heavy, it was important that the carts do not have to be manoeuvred over a ramp or step. As Esco’s BioPass mount straight to the client floor without any entrenchment needed (no ramps or steps), no manipulations to the standard entry design were needed.
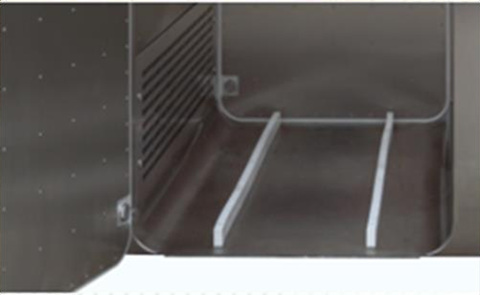
Figure 1. BioPass™ floor guides
Efficiently, Esco also utilised floor guides to aid the trolley through the chamber; making it more user friendly while minimizing the risk of internal damage, as heavy loads are moved through.
Another client requirement is for the system to both run in once- through (single pass) and recirculating airflow.
Standard units offer once-through (single-pass) airflow only but the team was able to install additional vents so the unit can be switched to recirculating mode during its gassing cycle.
The addition of vents was a simple procedure but was made complicated due to the facility’s limited space.
However, one of the main advantages was that our integrated catalytic converter does not require HVAC connections, rather, only power and compressed air.
Other features of the equipment are the HMI controller and electronic data recording for 21 CFR Part 11 compliance. This has been reviewed by Esco’s in-house engineers to ensure that it only took up minimal space without compromising on function or integrity.
The numerous alterations required to our standard design resulted in a close and collaborative relationship with our client. In providing them with the customized equipment, we have demonstrated our adaptability for other projects and machinery needs.
We enjoyed the challenges and look forward to exceeding the expectations of future clients.
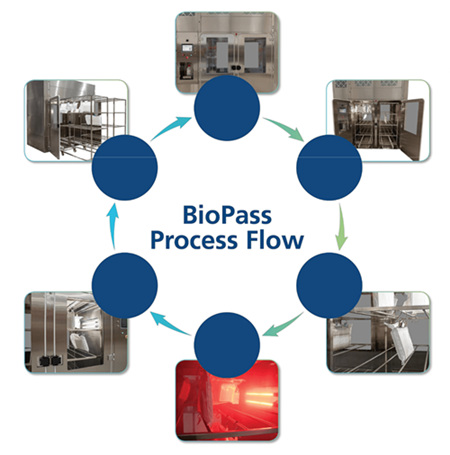